Petrochemical
Global Leader in Energy Selects Aera Decision Cloud™
to Improve Supply Chain Visibility and Shipping Performance
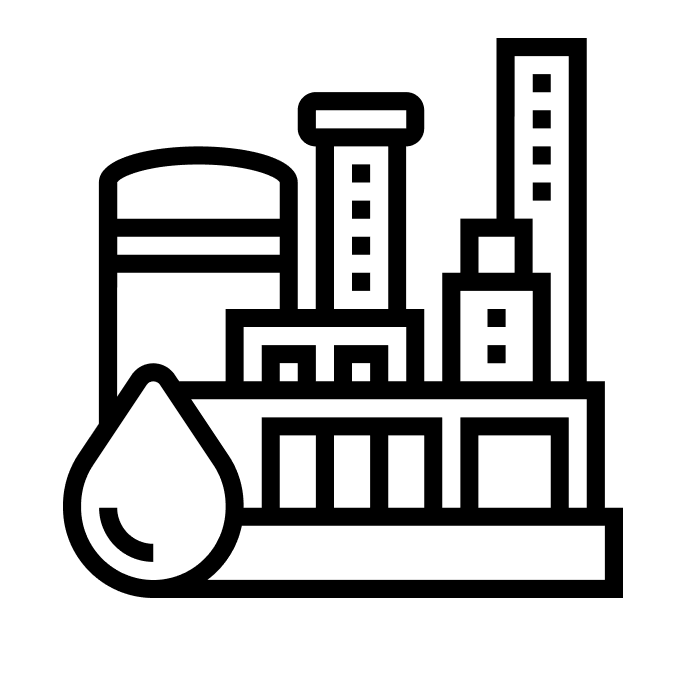
One of the world’s largest publicly-traded energy providers and chemical manufacturers, the company markets fuels, lubricants, and chemicals. It also develops and applies next-generation technologies to help safely and responsibly meet the world’s growing needs for energy and high-quality chemical products.
Business Need
Gain real-time visibility across the company’s entire supply chain (including areas managed by third-party partners) in order to improve shipping performance.
Results
- Increased on-time delivery and customer satisfaction
- Logistics and data network optimization
- Improved ability to track execution vs. plan
- Better communication with third-party partners
The Challenges
Worldwide demand for chemicals is expected to rise by 45% by the end of the decade, and rising living standards are driving demand for consumer goods and packaging – all of which require chemicals. As a result, leaders identified greater supply chain visibility as a crucial need in order to meet the expected growth in demand.
However, existing issues with traditional IT solutions presented challenges for decision makers. These systems operated with batch updates instead of real-time data. In addition, data was siloed and not digitized, and there was a lack of effective communication between groups.
The company needed real-time integration utilizing new technology, as well as new processes for more efficient and effective coordination.
The Solution
The company adopted Aera Decision Cloud™ and implemented the Outbound Operations Management Skill, which offers a workbench to track non-conformance in shipping in an exception dashboard, as well as the ability to execute corrections.
As a result, data was harmonized from order to delivery on the platform – incorporating actual and planned data from third-party partners. Decision makers could now leverage historical data to train algorithm recommendations, and create risk categories to prioritize and drive proactive communications when shipments were delayed.
Finally, the shipping process was overhauled to address issues that had caused visibility gaps. This redesign included addressing offline and ad-hoc communications with partners. The company selected champions and created a cross-functional community approach to improve communications.
“Our transportation specialist sees only the critical cases which are getting highlighted. Instead of spending time searching for issues, they are displayed based on predefined logic, comparing the plan versus actual performance and driving proactive communication with our customers.”
- Logistics distribution process advisor, global petrochemical company
Results
With improved visibility, shipments can now be monitored throughout the entire process – from order entry, to transportation planning, tendering, and shipment creation, over to slot booking, actual loading, and delivery of goods to customers. The decision trees the company implemented are driving the overall status and performance against the initial plan, as well as identifying critical cases that need to be managed.
In the future, the Aera Outbound Operations Management Skill will be expanded by incorporating additional source data used to drive predictions and recommendations, such as real-time truck visibility data. Also, the company is looking at opportunities to improve and optimize supply chain performance across process areas for specific business lines and regions.