Manufacturing
Global steel producer chooses Aera Decision Cloud™ to transform supply chain and customer experience
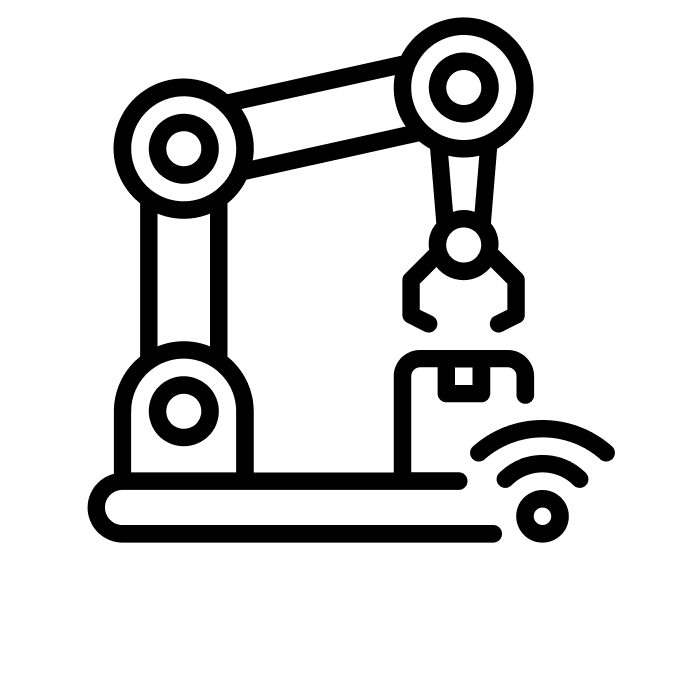
Since 1952, family-owned and operated international steel producer DeAcero has continued to drive innovation. With a production model relying on scrap, not CO2-producing iron ore, DeAcero has built a multi-billion dollar, integrated steel recycling and manufacturing company. Their product and services portfolio includes 9,000 product SKUs across six categories and seven vertical markets with 90 industrial sub-sectors.
Business Need
A customer-centric, dynamic operations model to improve the perfect order metric and overall customer experience
Results
- Improved perfect order service metric by 1-2 percentage points each month since December 2021
- Gained end-to-end visibility across the order management process
- Broke through functional silos with better visibility and access to quality data
- Eliminated the manual effort and analysis required to identify risks and evaluate alternatives
- Gained faster risk remediation through automatic writeback of key actions in DeAcero’s source system
The Challenges
DeAcero’s immediate goal was improving its order management process — specifically, any delayed orders and orders that were at risk of being delayed — and increasing its perfect order service metric. The company also wanted to improve its customer service through better, more immediate communications with customers throughout the order lifecycle.
Also, the company needed the ability to inform customers about order status, quickly determine whether there are product substitutes if inventory or logistic issues occur, and continue to align throughout the order lifecycle. At the same time, DeAcero was growing quickly, with independent and homegrown enterprise resource planning (ERP) solutions in place. A key challenge was access to reliable data and the ability to analyze and respond to issues proactively.
DeAcero needed real-time visibility across internal processes and better, quicker access to data with the tools to manage data in a better way to improve planning and make faster decisions.
The Solution
After considering multiple supply chain management and planning solutions, DeAcero chose Aera Decision Cloud. The first phase of the project focused on improving visibility and proactive response across sales orders in Mexico for the company’s Mesh & Wire division, one of DeAcero’s largest — representing nearly 60% of its total sales orders worldwide.
A tailored solution was created, built on the Aera Decision Cloud platform hosted on the Amazon Web Services (AWS) cloud infrastructure, and focused on preventing service risks and improving order management throughout the lifecycle of every customer order. This project included developing an Order Lifecycle Management Skill; building a digital control tower; and training a DeAcero team of Skill builders and business users to develop and advance both the Skill and these capabilities within the platform.
The Order Lifecycle Management Skill is designed to sense when an order may be late due to inventory shortage. It then assigns a root cause of inventory availability to provide visibility to the inventory impact on a delayed shipment and recommend solutions. This Skill understands and considers specific events in DeAcero’s order-to-delivery process that can make a difference between on-time and late deliveries for each unique order and shipment.
“We are just starting our digital journey to transform our supply chain processes and management. Through Aera Decision Cloud and the power of our collaborative DeAcero-Aera team, we are accelerating our learnings and improving our ability to be proactive and predictive.”
- Raul Gutierrez, VP Supply Chain, DeAcero Group, CEO, DeAcero Logistics
Results
Through partnership with Aera, DeAcero has gained the technology and tools to become more agile and adaptable, and to align more closely with customers. Today, DeAcero can continually monitor estimates for customer delivery dates throughout an order’s lifecycle. Risks to on-time delivery are identified, and specific decisions can be automatically recommended to address the risk. DeAcero has also improved visibility into issues and has reduced the amount of time spent on addressing them.
At the same time, the company is becoming more resilient and reliable. DeAcero now has a trained team of Aera Skill builders, as well as business users leveraging the platform’s Discovery capability to build their own reports and dashboards.